Swedish e-bike firm Cake discuss progress towards zero carbon
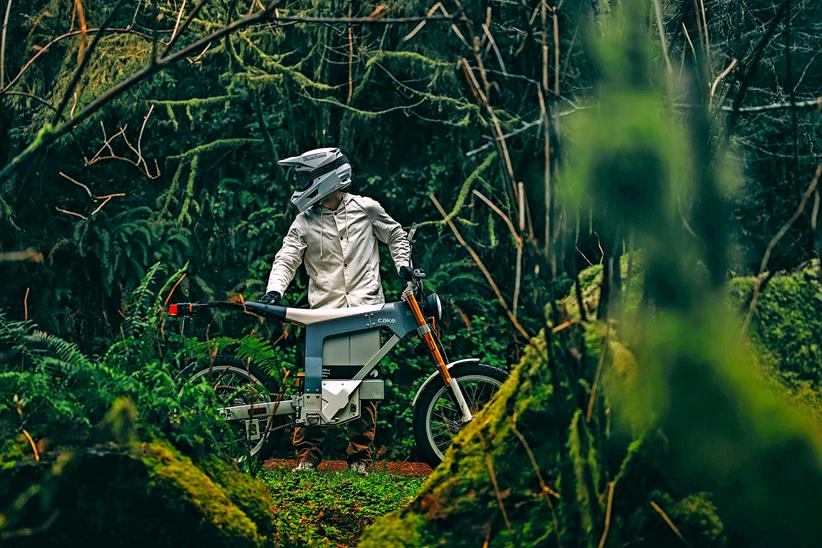
Cake Motorcycles founder Stefan Ytterborn has updated MCN on plans to build the first truly fossil-free bike by 2025.
The Swedish firm calculate that building one of their electric-enduro-style Kalk ORs produces about 1.2 tonnes of carbon dioxide but working with energy company Vattenfall they hope to inspire others to make the change. And the latest news is that Öhlins have come onboard to provide the forks and shock for the eco-machine.
“It’s moving at pretty high speed,” Ytterborn told MCN. “We’re potentially going to make the actual bike in fossil-free steel, instead of doing it in aluminium.
“There’s a lot of chasing and tracing materials – both virgin materials as well as finding treasures of recycled material that we can re-activate, so it’s a really exciting process.
“It’s one of the projects where we invest the most time and resources and again, I would say we would never be able to do a project like this unless we had Vattenfall behind us, because the level of resources being invested is far beyond what our own ability would’ve been.”
Ytterborn says that between five and 10 firms a week are now making contact to get involved, but he recognises there are still plenty of difficult hurdles to overcome.
The firm are now in talks with the owners of a disused copper mine in northern Sweden which could be used to supply motor parts and wiring in general. Bigger challenges in the zero carbon quest will include circuit boards and tyres but Ytterborn remains optimistic.
Baking a fossil-free Cake mix: Swedish firm aim to eradicate fossil fuels in the production line by 2025
First published on 8 September 2022
Electric motorcycles may have the upper hand over the internal combustion engine by producing no emissions at the tailpipe, but there is still a sizable amount of pollution created in the production process – be that in the assembly, the mining of raw materials, or the process of battery production itself.
Lightweight Swedish electric bike firm Cake are acutely aware of this, and have now announced a new partnership with European energy company Vattenfall in an attempt to build the first truly fossil-free electric motorbike by 2025.
“We would never pound our chests and say: ‘Hey, look at us, we’re sustainable because we’re electric.’ There’s so much more to sustainability,” Cake founder Stefan Ytterborn told MCN. “It’s wonderful to team up with such a chunky organisation and share that perspective. Without them it couldn’t make it happen.”
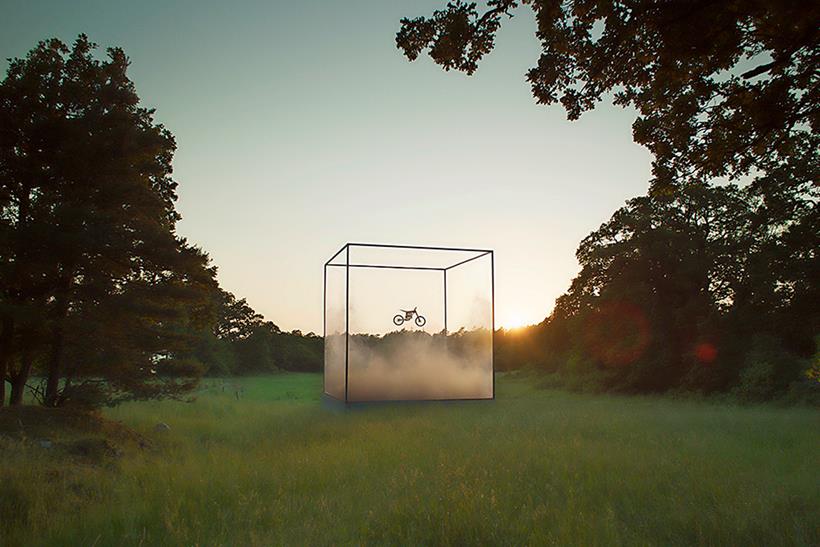
The first step has been to calculate the level of carbon dioxide currently produced in the manufacture of one their electric-enduro-style Kalk OR models. The Swedish firm calculated this is 637 cubic metres, or about 1.2 tonnes – the same amount of pollution, they say, as someone flying from London to New York and back twice.
However, diagnosing the issue and tackling it are two very different things, with every element of the process – including the way raw materials are extracted and the fuels used to power factories – needing to be scrutinised.
“A big part of what will be done and the most important bit of decarbonisation is of course to electrify and then plug-in green energy,” says Isabella Pehrsson, Head of Sustainability and Project Leader on the Cleanest Dirt Bike Ever project. “Materials need to be from a non-fossil source,” she continued. “You cannot use oil and then call them ‘fossil free’ at the end. When it’s taken from the ground, every chemical that is added to make something like aluminium will need to be considered.
“It’s how those additives were produced, how it was transported and how it was processed to become a material,” says Isabella. “All of those aspects will be taken into account to decarbonise. And all those processes will rely on green energy to be decarbonised.”
Cake say the elements being looked at to become fossil-free include aluminium, steel, plastic, rubber, plus the controller, motor, battery, brakes, suspension, and electronics. Their partners, Vattenfall, have already begun some of the development work here. Pehrsson explained: “Vattenfall is one of the parties that recently created the world’s first fossil free steel. This will be in the bike, we’re setting up that collaboration now.
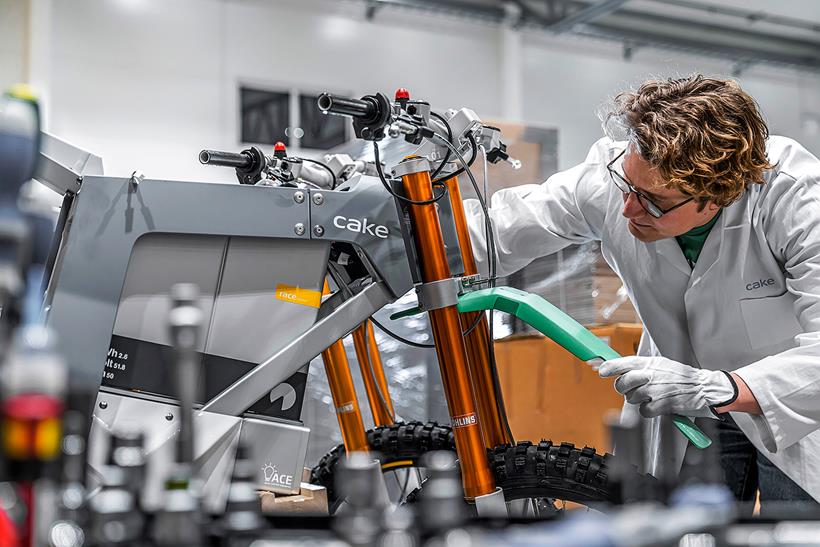
“They are working with Cake because we’re a fun product utilising materials that are widely used in the industry,” she added.
Cake’s eco plans in detail
Splinter cell: The firm continue to keep their cards close to their chest surrounding battery development at this stage, but have said that they don’t have the capacity to produce cells for batteries in house, so will need to find a sustainable partner.
Boxing clever: To demonstrate the production carbon footprint, Cake strapped a Kalk OR model inside an 8.6m high cube, which represents the volume of carbon emissions produced during manufacture.
The Cake mix: Cake’s production facility just outside Stockholm runs on solar energy. The firm are expecting to produce 25% of all parts in house by 2025 – although they have not yet decided which of those parts it will be.
Vision for a greener future: Cake founder Stefan Ytterborn told MCN: “We will never reach 100% zero emissions, [but] it’s a way of accelerating to a much better collective perspective, between the industry and the users, to accelerate our level of purpose. We [will] launch the first commercial bike by 2025 that’s come as far as we can get towards zero emission. That one will be the best that there is from us.”
Cutting carbon footprints with Cake: Swedish firm evaluate paper-based replacement for plastic components
First published on 17 June 2022 by Ben Purvis
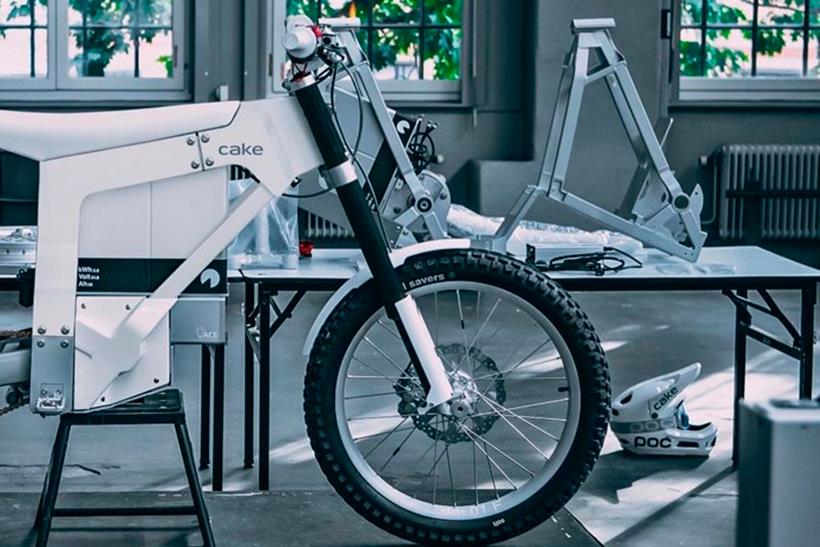
The drive towards a carbon-neutral future has long focused on the direct emissions of engines and the shift to electric power but even the complete elimination of exhaust fumes is only a partial step towards a greener future.
For a more complete solution firms need to reduce the emissions from manufacturing – and Swedish e-bike firm Cake is looking at replacing plastic parts with paper to achieve that.
The company have joined forces with fellow Swedes at PaperShell AB, a start-up focused on turning paper into a durable, wood-like material that can be moulded like plastic or carbon fibre.
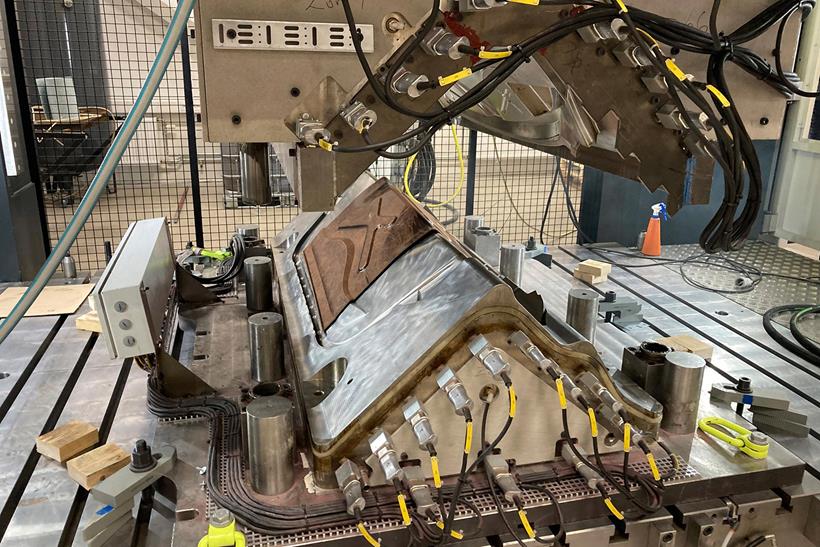
Despite its roots in paper, the final material is a water-repellent and fire-resistant cellulose fibre. This allows it to be used in both wet and hot environments without the need to add flame retardant chemicals, and promises a combination of strength and density that should allow it to be both tough and lightweight when replacing plastic.
“PaperShell aims to make components that are more environmentally friendly than press moulded veneer, as weather-resistant as plastic and strong as fibre composites,” said the company.
The material is sculpted by press moulding, where it’s clamped between two shaped moulds under pressure to form its final, three-dimensional shape, or bladder moulding where it’s put into a female mould and an inflatable bladder is inserted to force it towards the walls of the mould.
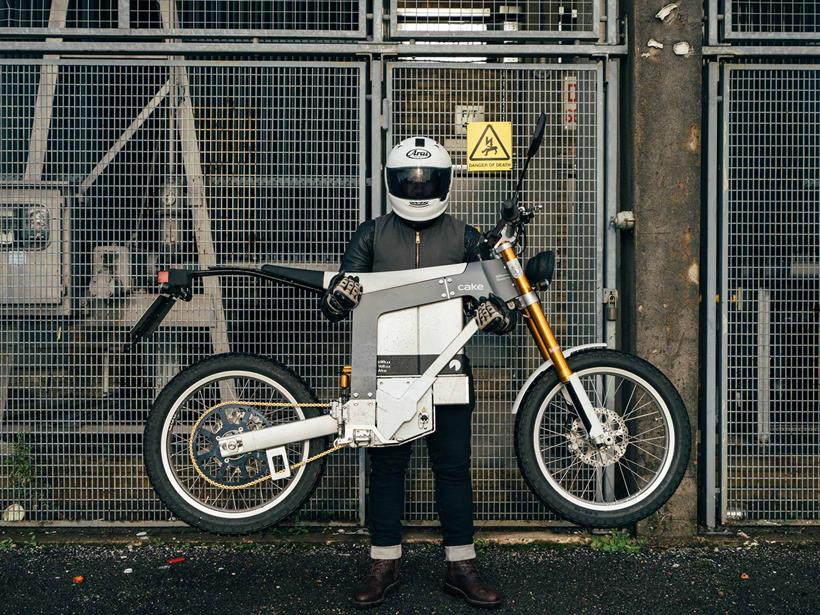
Like plastic, it can also be moulded with a variety of finishes – gloss, satin, matte, rough or patterned, with logos or pictures embossed into the surface if desired – and it can be either left with that surface or given a painted finish.
Unlike plastic, it’s also biodegradable over time, and it can be recycled in the same way as wood. PaperShell claims that its environmental impact is a fraction of that of more conventional materials. Measured by ‘kgCO2-equivalent per kg’ – a yardstick of the environmental impact including material production, manufacturing, and end-of-life – PaperShell comes in at 0.65 kgCO2-eq, compared to plastic such as polypropylene which rates 4.95 kgCO2-eq or glass-fibre reinforced plastic at 25.05 kgCO2-eq.
Stefan Ytterborn, founder and CEO of Cake, said: “We’re excited to work with PaperShell and hope that we can play a crucial part in finding a material that can minimise or even eradicate the use of conventional plastics in our motorcycles. This is a collaboration that ultimately will benefit the entire vehicle industry and beyond.”
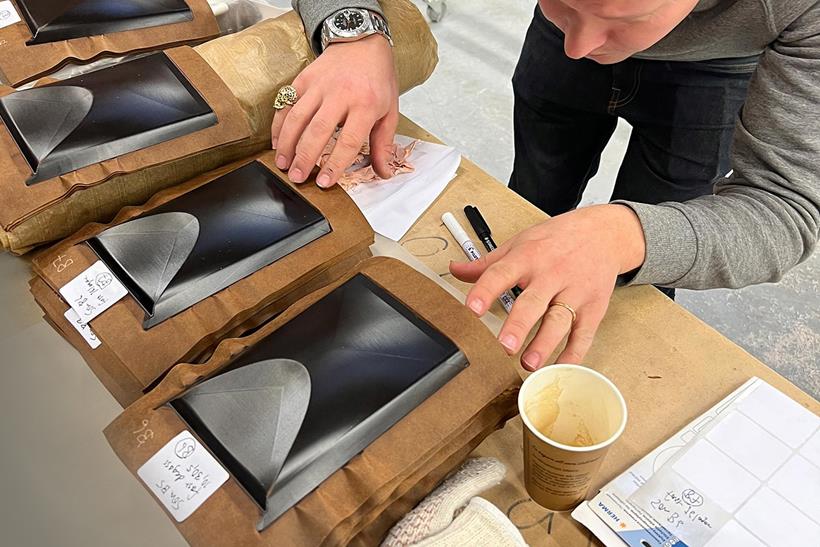
Although the initial focus is on replacing plastic components, PaperShell’s weight-to-strength ratio may also allow some metal parts to be switched to the new material. Although only half as strong as aluminium, it’s also half the weight, so provided there’s space to increase a component’s thickness, parts that are made of aluminium could also be replaced with PaperShell versions.
PaperShell was only established in 2021, after three years of work on the idea, but the company’s pilot plant in Tibro, Sweden, can already make 60,000 components per year. In 2023, the company plan to open a flexible manufacturing plant that can turn out more than ten times that many, annually churning out as many as 700,000 planet-friendly parts.
Some will eventually be destined for motorcycles, and by 2025 Cake hope to use PaperShell components to develop a bike with the smallest possible carbon footprint.
Anders Breitholtz, CEO at PaperShell, said: “We can’t think of a more perfectly challenging testbed for our material than the industry-leading electric off-road motorcycle and look forward to developing further PaperShell’s inherent resistance to fluids, UV-radiation, weather and fire.”