British firm Rheon Labs uses NASA tech to create flexible and lightweight body armour
Rheon Labs have developed a new range of comfort-focussed motorcycle armour using technology originally designed to be deployed on NASA Space Shuttles.
The British company, based in Battersea, London, are now producing armour for Mosko Moto’s Boundary and Basilisk product lines and also work with Roadskin, and Harley-Davidson, as well as supplying energy absorbing lining tech for Ruroc helmets.
The armour has been produced with the aim of being the most comfortable on the market – allowing the rider to remain protected without the feel of bulky protectors on their extremities. This is ideal for adventure riders spending plenty of hours in the saddle, both on- and off-road.
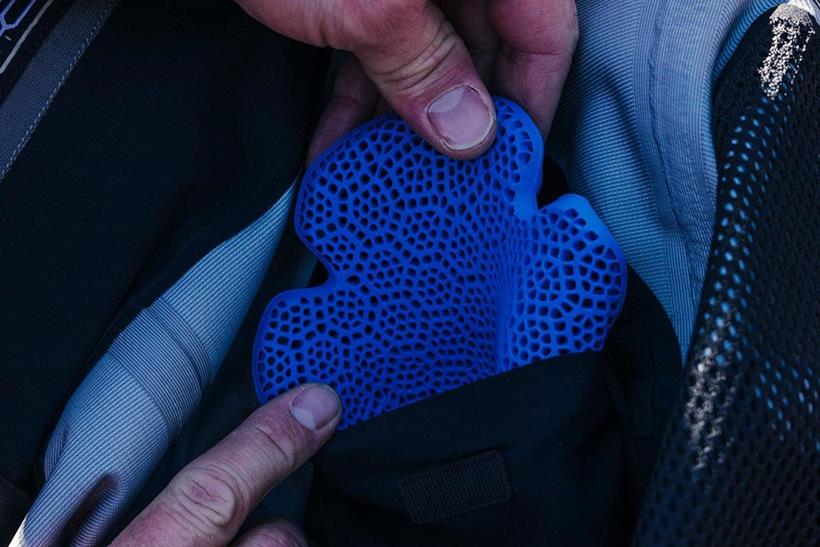
Starting point
Rheon was developed by Dr Daniel Plant when working on a NASA project looking at foam replacements in the Space Shuttle. He then spent the next 15 years refining the idea at Imperial College, London, before branching out to form Rheon Labs.
“Dan, our founder, was a super keen motocross rider, as well as mountain bike riding – kind of anything dangerous – so that’s why we started in there. It was just a real obvious area where we thought we could do a great job and the technology lends itself to it,” said marketing chief, Ben Scott.
Rheon produce products for the shoulders, elbows, knees, central back, full back, chest, knuckles, and ankles – employing the use of what’s known as a non-Newtonian material (meaning it has a variable characteristics dependent on stress, a bit like D3O) allowing it to remain soft until there’s an impact.
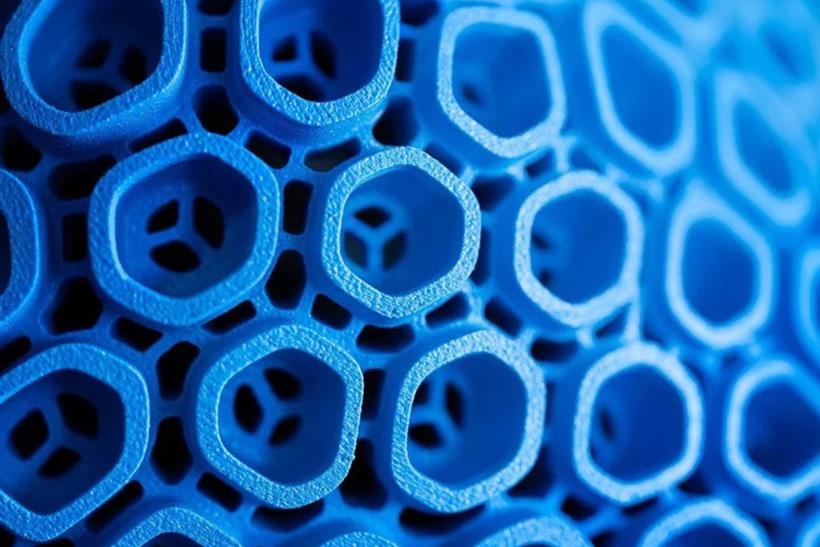
Using cell structures inspired by nature, the patented design then stiffens up to absorb the impact of an accident, to reduce the energy transfer to the rider and limit the risk of injury. Rheon began looking into the idea of impact protectors for clothing around three years ago.
With the material capable of passing CE testing with a thickness of less than 4mm, Rheon can produce kit with either Level-1 or Level-2 protective qualities – employing a grid-like cell structure that allows ventilation, as well as pushing more material into a point of impact in an incident.
Comfort focus
“What suited Rheon best was attacking comfort – so something that’s so comfortable that it essentially disappears in their garment,” Product Manager, Paul Farrar told MCN.
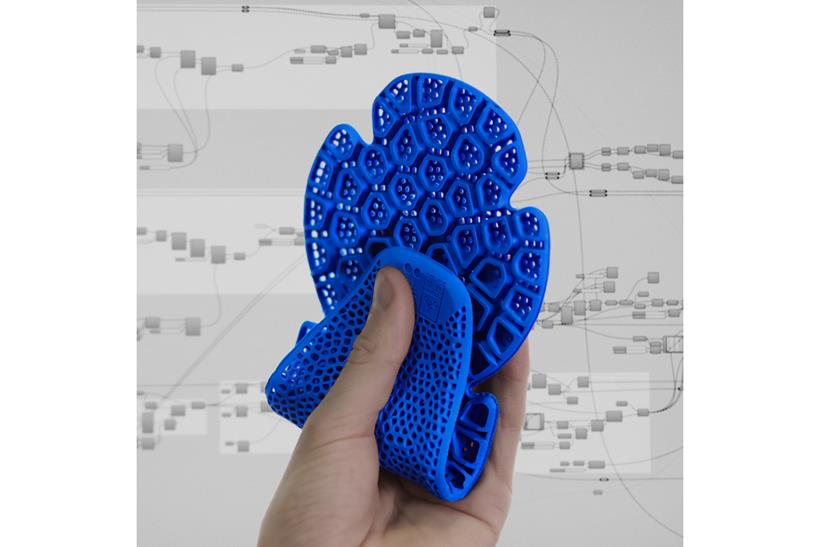
“We set a product vision of creating invisible body armour and went after that. It passes all the CE standards, gives you great impact protection, but gives you that comfort, which has the biggest influence on the rider experience.
“There’s stuff out there that does great numbers in the lab, but people don’t even put them in the pockets of their jacket because it’s just too bulky, hot and heavy – in which case it’s absolutely useless.”
On top of a focus on comfort, the brand also employs specialist experts to develop products that suit the specific needs of motorcyclists. This includes Chief of Design Olga Kravchenko, who is a teaching fellow at the Dyson School of Design and has spent over a decade codifying and exploring algorithmic design techniques.
“We can put in things like sweat maps, heat maps, bone density and it creates these shapes. That’s not just for aesthetics,” Scott continued. “It’s super lightweight, super breathable and that comes from that data that’s fed in.”