Inside the factory where HEL Performance create braided lines, race‑spec calipers and much more
Paid partnership with HEL Performance
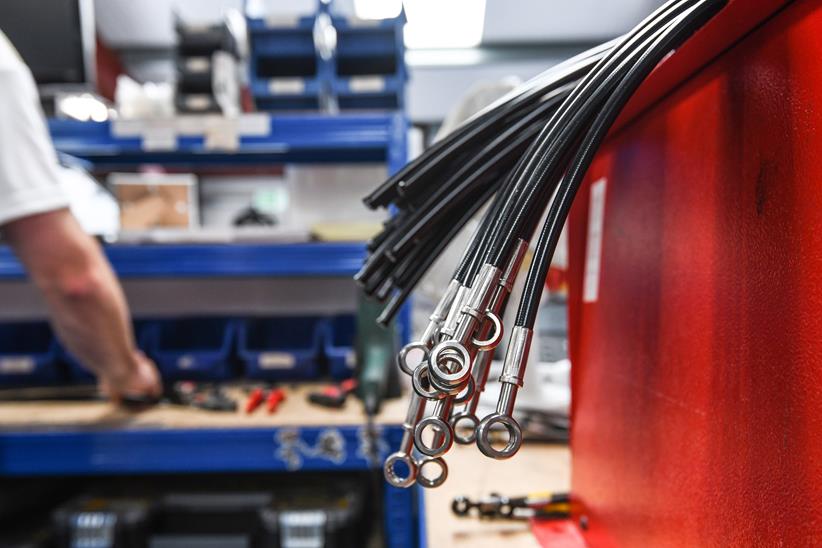
Exeter-based HEL Performance work around the clock creating braided brake lines, race‑spec calipers, master cylinders and much more.
HEL make more than 500,000 brake lines every year. That’s 155 miles of brake hose. They machine their way through almost 100,000 metres of stainless steel bar (over 60 miles) – their 18 CNC machines run 24 hours a day, seven days a week, and churn out over three million banjos, ferrules, bolts and various other fittings every year. That’s quite a few.
Same product no matter who
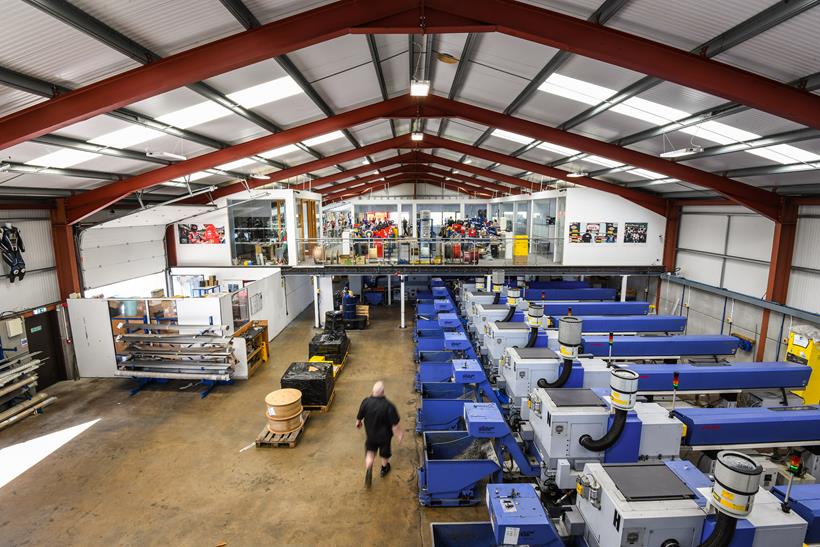
These sliding-head CNC machines produce all the brake line fittings, including banjos, ferrules and bolts. The business started in 1999, initially making hoses for hydraulics on tractors. “I’ve always loved motorbikes, so I wanted to do something with bikes that was connected with hydraulics,” says managing director Simon Lane.
“I went for brake hoses. The company was called Hose Equip Limited, which is where HEL came from. For 20 years we’ve had double-digit growth, year on year. We supply MotoGP, World Superbikes, British Superbikes, motocross, road riders…
“Products that we supply to MotoGP are exactly the same as what we supply to a customer on the road – there is no difference. And they’re the same as at the Isle of Man TT. There’s always that mind on quality because we’ve got people going down Bray Hill at 180mph with our product on.”
All year round
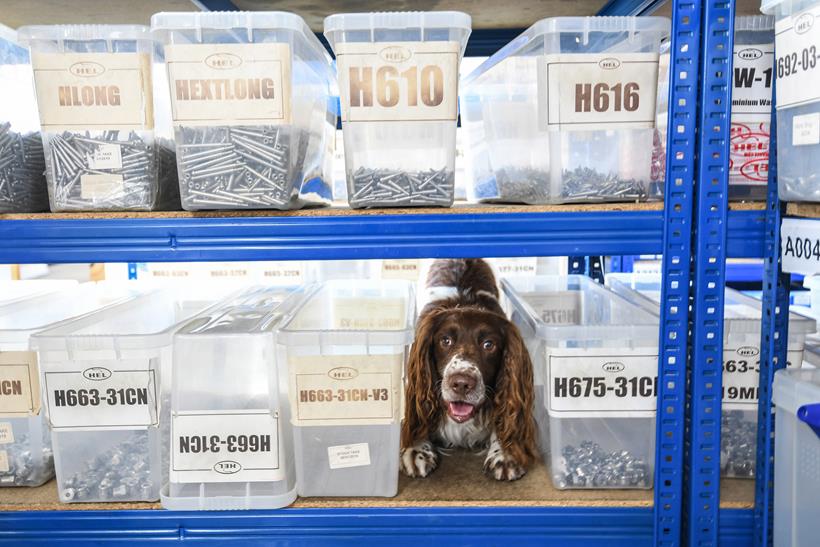
Clearly keen to ham it up for the camera, Simmi the HEL dog works their way in among the very many parts held in the stores and dispatch area. As export manager, Simmi’s owner Nick Weston spends a lot of his time in stores picking and packing parts for agents and customers.
“In the morning I’ll get all the emails sorted out, get the orders on the system and then start picking, boxing and getting it packed up,” says Weston. “The biggest countries [for our parts] are Germany, Australia and Poland.
“We’re in New Zealand, Serbia, Estonia, South Africa… We have a primary agent in each country. The export side of it just doesn’t stop, because you’re following the summer around the globe – when it’s winter over in America it’s summer in Australia or New Zealand. It is non-stop,” says Weston, rushing off to pack another order. Probably for Kazakhstan.
It’s a steel
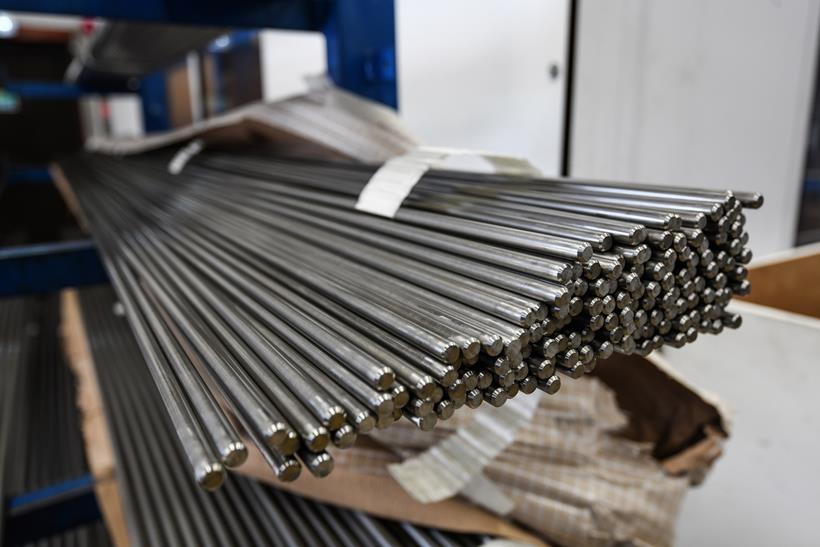
Very many lengths of 14mm diameter 303-grade stainless steel – known for excellent machineability – waiting politely to be transformed into male and female nuts, ready to be used on lines with anti-lock brakes – they screw into the ABS blocks.
“Our main stainless steel fittings are made here,” explains Simon Lane. “We buy the material from a UK company that has a Spanish mill, so we get mill certification, and our aluminium comes from a German aerospace company called BIKAR.”
Not an Amstrad
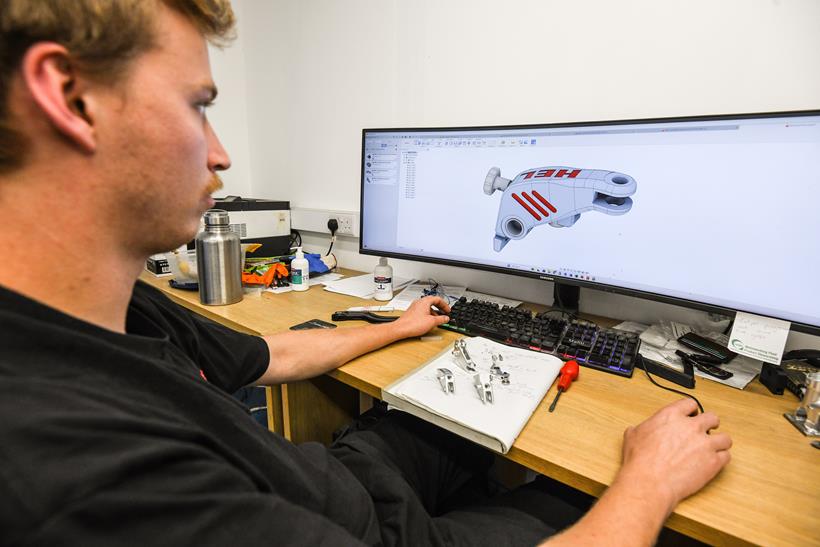
“This is a prototype part essentially, for our newer generation of master cylinders which haven’t come out yet,” says CNC machinist Andy Crew as he drives the state-of-the-art CAD (computer aided design) software.
“Everything gets drawn up in CAD as a 3D model by a designer; we then use the model to generate the tool paths and code that the CNC (computer numerical control) machines can understand. We can simulate what the machine is going to do. Once you’re happy, that’s when you start production runs.”
Precise quality
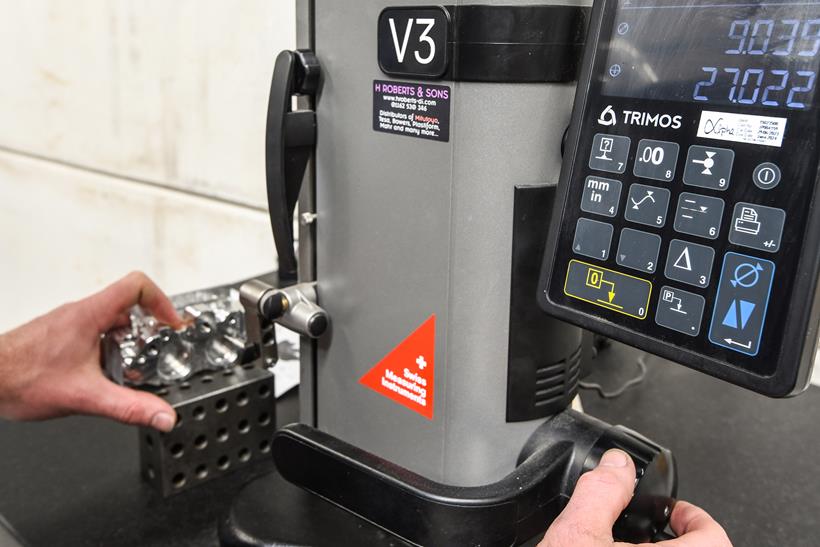
“This is our Trimos vertical height gauge,” says machinist Tom Lee-Parker. “You can use it to measure for all sorts. We use it to check holes to the drawing – it’s accurate to a micron. It allows us to accurately check all the dimensions on the drawing – we have verniers and pins, but this gauge helps us measure positions.”
Metal candy floss
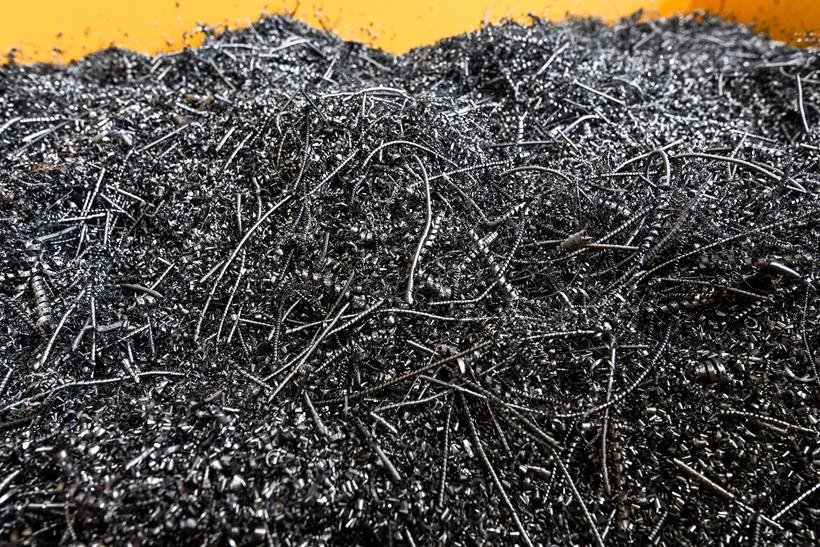
If you’ve never been into a machine shop, there’s something curiously fabulous about massive piles of swarf (the by-product of the machining). And with machines working round the clock, there’s a huge amount of swarf left after all of HEL’s various different processes. Roughly 80 tonnes of stainless steel swarf is produced each year – which is all recycled into new bars, ready to be made into parts again. Motorcycling: leading the way in green manufacturing…
It’s all very clever
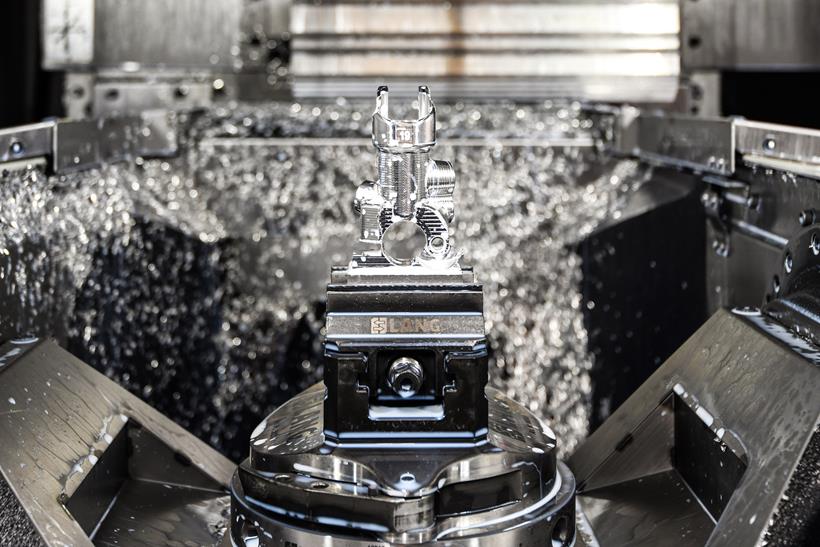
A freshly-made master cylinder sits inside one of HEL’s numerous CNC milling machines. “This machine is doing our very first batch of Gen-2 master cylinders that haven’t even been released yet,” says Tom Lee-Parker, one of the CNC machinists, who’s responsible for programming, fixture design, machining and setting up machines. Robot loaders feed billet aluminium blocks into the machine tools with absolute precision.
“The machines run 24 hours a day. The robots are great, we can make parts very fast – you can arrive in the morning and go, ‘wow, we’ve got 30 calipers ready to go’. These machines all have tool checking on them – it will measure its own tool and if it’s out within 0.1mm it will go, ‘this is wrong, stop cutting’.”
For the love of stoppers
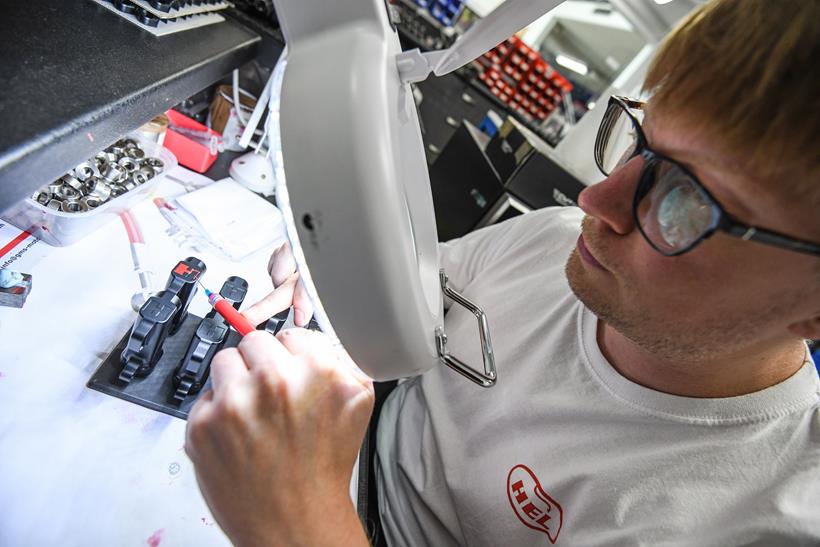
Technical assembly engineer, Adam Powell, delicately paints the HEL logo onto a master cylinder. “It’s a high-temperature caliper paint that we use – we know it’s not going to flake or damage,” says Powell, his sight focused through the magnifying glass.
“If people want white or black, we can accommodate – we can do custom colours. Any aluminium products that have been anodised come to me in this room, and are assembled to make the finished product. We take our time because it has to be done right.
“They’re brakes – and if they go wrong it could be someone’s life. Anything that doesn’t fit gets discarded and recycled – we want to be beyond perfect.” Powell has only been at HEL less than a year but feels lucky, admitting it’s a dream occupation: “This is my forever job.”
Opposite of stuffy
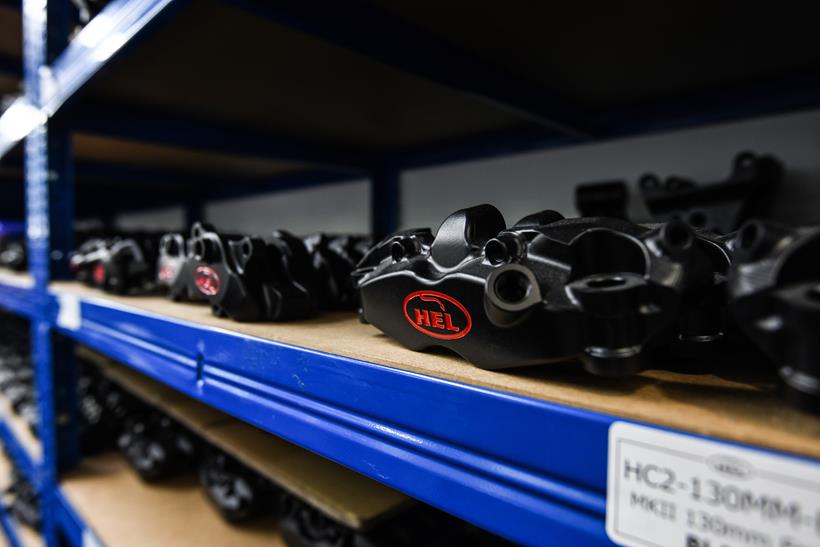
The main entrance and reception area is refreshingly laid-back, and packed with racing memorabilia, signed prints from race teams… and a pool table (this is managing director Simon Lane shooting a few frames with Jai Campbell).
The business started in Totnes and is now based in Exeter. Never straying from Devon, it’s become a bit of a company policy to keep things local.
“We’re very passionate about things from within our area,” says Simon. “We use a local anodiser and as many local firms as we can – our lubricants and oils come from Okehampton, for example. We try to use as much as we can locally, and we even sponsor our local football team.”
Speed… with precision
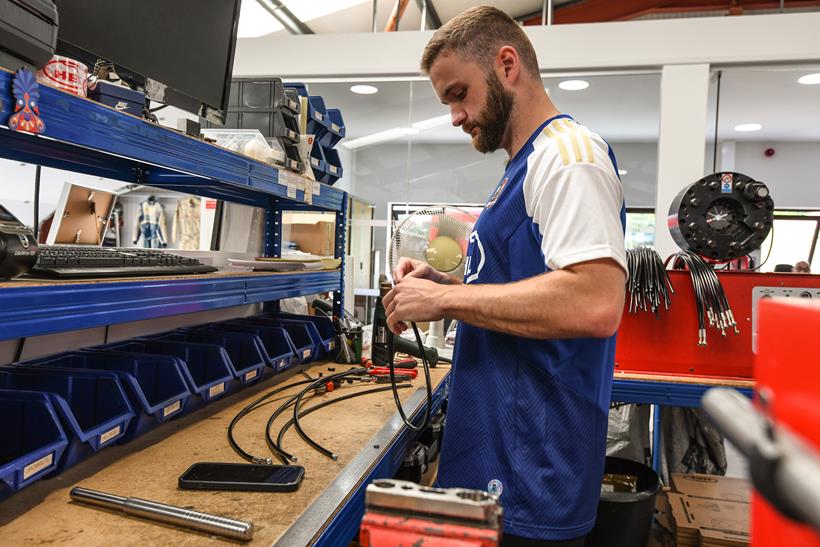
Jai Campbell assembling brake lines at his workstation. As a worktop technician, Jai has his workspace laid out to perfection so that he can be as efficient as possible. Colleague Becky Trechmann-Vance has a similar setup.
“I’ve got a little system,” she says. “Everything is laid out as I want it so that I don’t even have to think about where I’m reaching. For different customer brake lines I can do 25-30 a day, but if we’ve got a big order of all the same hose you can do 50-100 in a day.”
It’s ever-changing
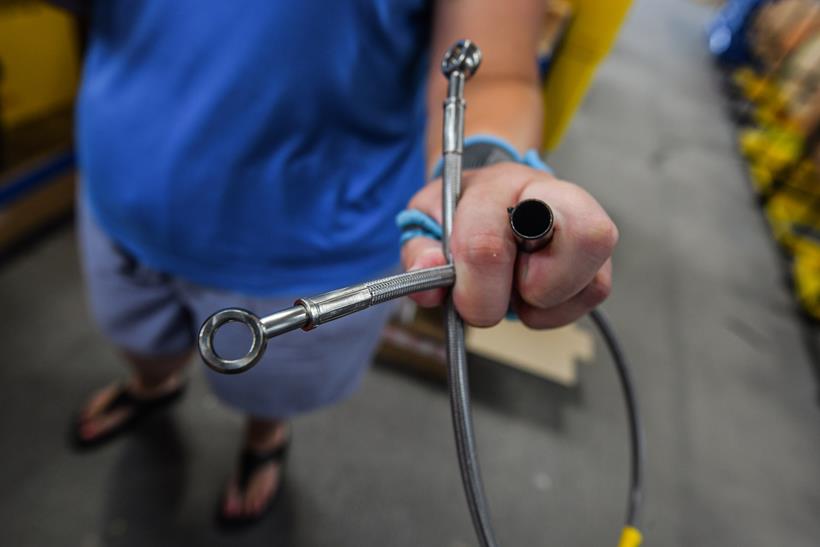
Becky Trechmann-Vance with one of her newly made brake lines. “We keep our regular parts ready on our benches. We bring up the specific hose spec on the system, bend the banjos or fittings to what we need, then cut the hose and put it together. It’s a mixture all the time.
“We get our big orders because we have contracts with some large companies, doing a hundred of the same hose – and then other days you’re doing customer orders through our website. And then we have race teams that need replacements, so we’re doing stuff for them all the time.”
Buy top stuff…
Find lines, calipers, master cylinders, thumb brakes, and more at the HEL Performance website.
- Just so you know, we may receive a commission or other compensation from the links on this website - read why you should trust us.